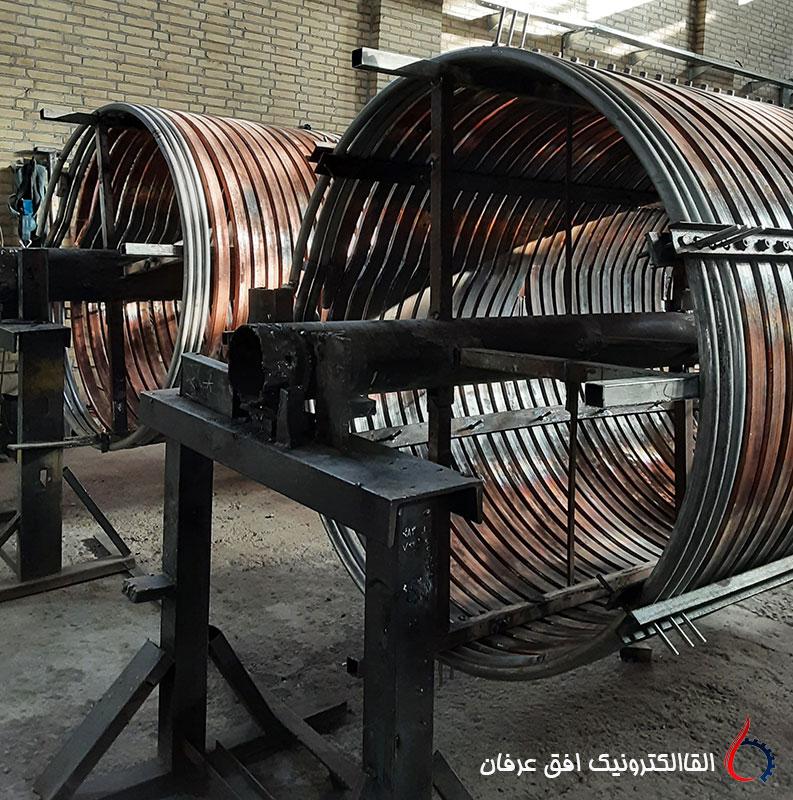
The central part of all induction furnaces is the copper coil, whose main role is to create a magnetic field, which creates eddy currents to heat and melt the scrap. The electrical and mechanical characteristics of the coil affect how it functions and the melting process.
Induction furnace coil structure
- Active part: This part generally consists of cans or copper tubes that are shaped in a circular shape. The task of this section is to pass the electric current created by the frequency converter board in order to create a magnetic field. The use of cans or copper pipes in this section is firstly for better passage of electric current and secondly to create the possibility of water circulation for the purpose of cooling the coil.
Inactive part: This part consists of cans or steel pipes, which are used for cooling the furnace soil at both the upper and lower ends of the coil, and in some special types, it is used as a half ring between the active parts.
Faraday ring or shorting ring: this part can also be the active part of the copper water pipe or copper tube, but with the difference that it is a single ring. This ring is placed at a distance from the active and inactive parts of the coil. In all types of induction furnaces, this ring is designed as a water-cooled copper plate.
Restraint system: This section includes steel or brass bolts that are welded to coil rings and then tied to FRP supports. This system has the task of restraining and preventing coil rings from deforming.
Isolation and insulation: This section is used for electrical insulation and preventing current leakage between active coil rings.
Electrical connections: These connections consist of copper sheets or conical beads made of copper and brass. The task of these connections is to inject electric power from the frequency converter board to the copper coil.
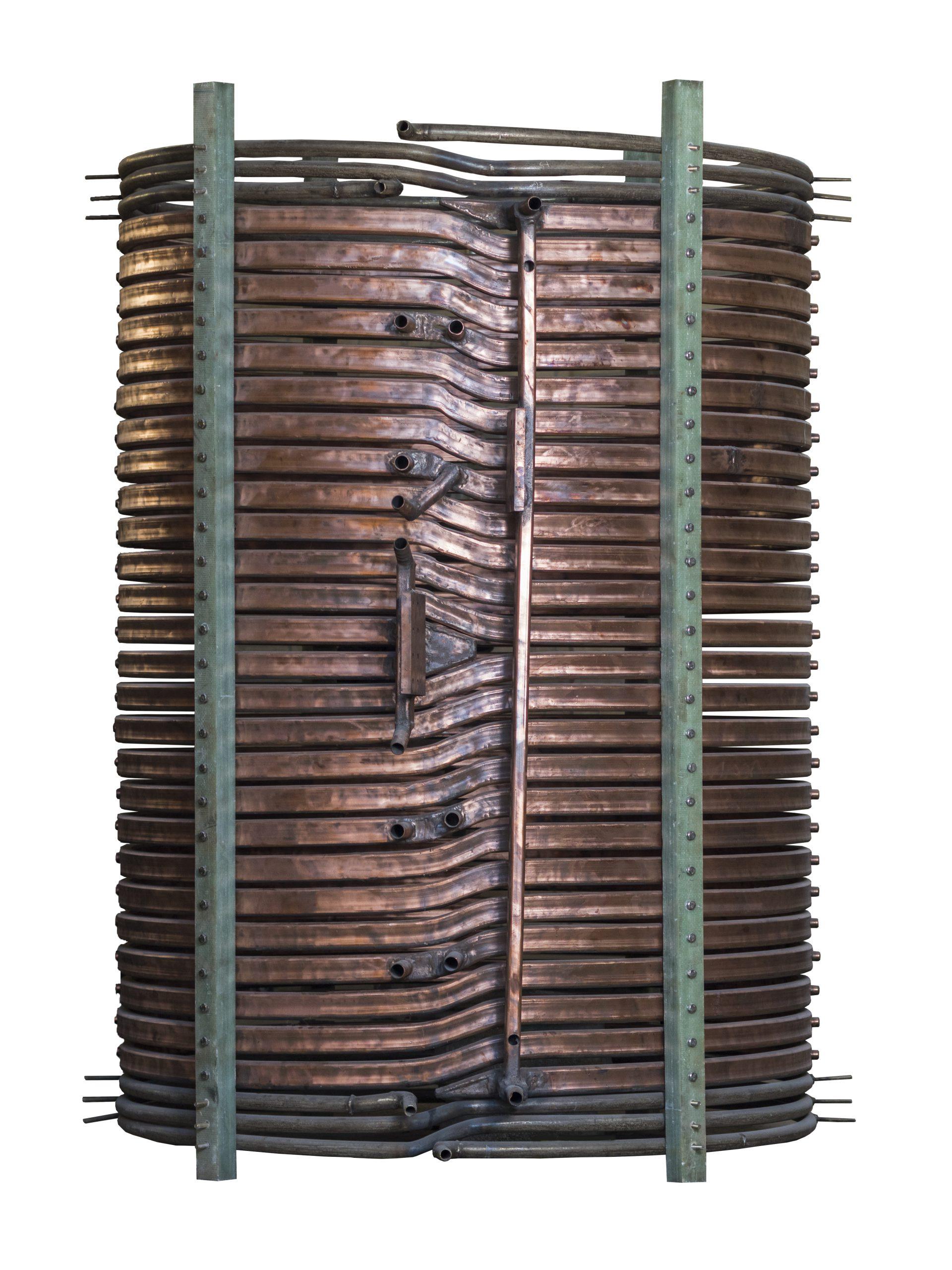
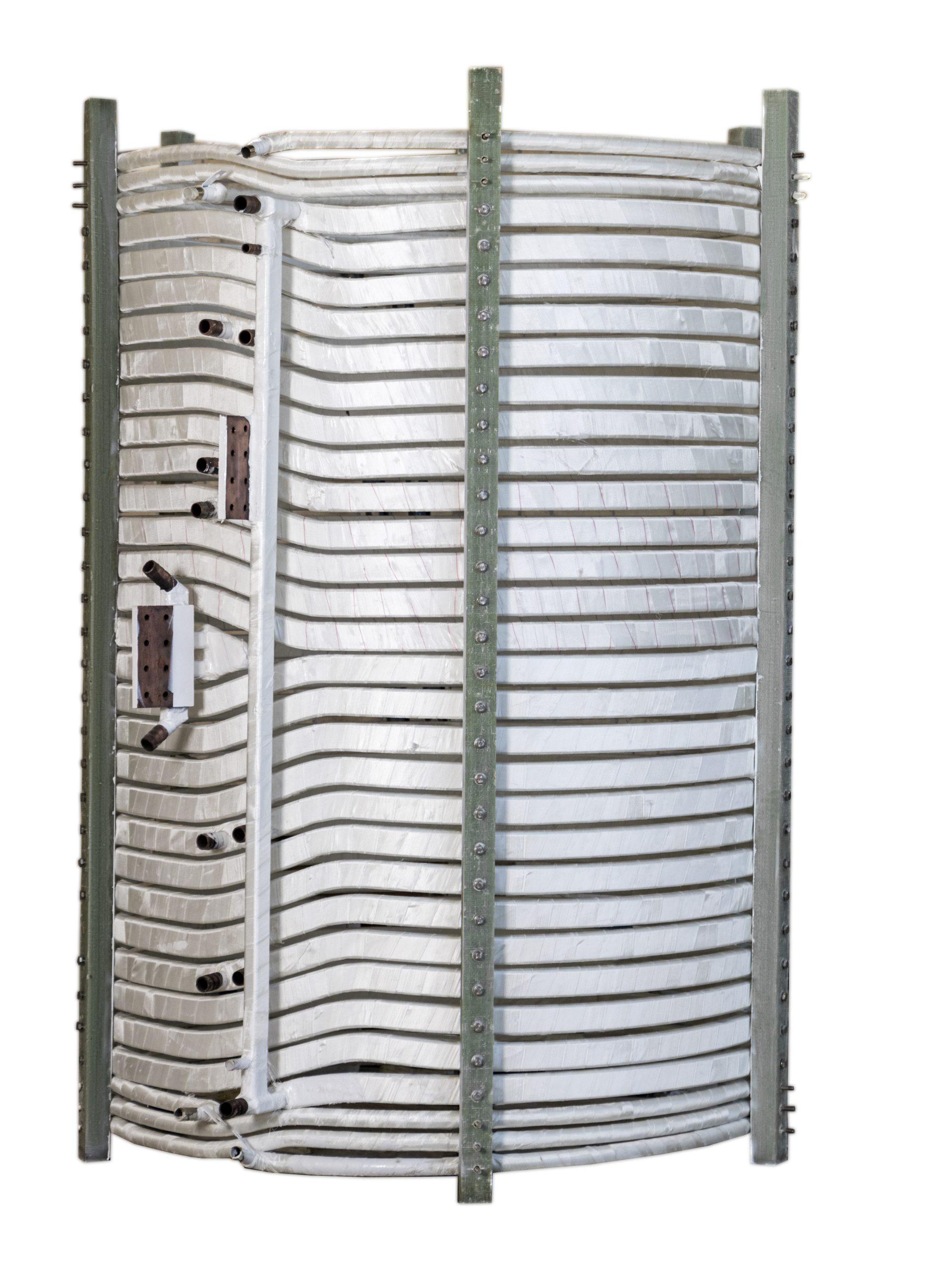
Types of induction furnace coils according to the way of twisting
Induction furnace coils are wound in two ways. The first method is helical coils that are wound spirally from the beginning to the end. These types of coils do not provide a balanced and uniform applied magnetic field and heat to the materials under melting due to the angularity of their rings, therefore, the use of this type of induction furnace coils is mainly construct and used in lower dimensions and power levels and not recommended to use them on a larger scale. Also, the presence of non-uniform distances between the active coil parts and the lack of parallelism between the two upper and lower surfaces of the coil are other problems in the assembly and operation of helical coils.
The second method is offset coils. Unlike helical types, these types of coils are made of flat rings that are wrapped in a kneeling (offset) shape to form a layer at the beginning and end of the rings. Therefore, in contrast to helical coils, in this category of coils, the upper and lower surfaces of coil is completely flat and parallel, and also applies a uniform magnetic field and heat to the material under melting, therefore, the use of this type of coil, especially in high powers and tonnages, is recommended.
Types of induction furnace coils according to assembly method
Induction furnace coils consist of one or more active parts, which are placed in parallel with each other. The active parts in the copper coils can be parallel to each other in two consecutive and two threads ways.
In the coils that are designed with consecutive actives, the active coil sections are placed sequentially and coaxially in one direction and are connected to each other, and finally either are electrically parallel to each other by using busbars on the coil or with the connections of the corresponding water cables.
In this case, the rate of coupling between two consecutive active parts is usually 20 to 40%.
In coils with double threads actives (which is usually common in coils with two active sections), the active sections are interwoven with each other, so that their rings are placed alternate way. In this case, the rate of coupling between the two parts of the active coil is close to 100%.
It should be mentioned that generally the two threads coils are wound helically.
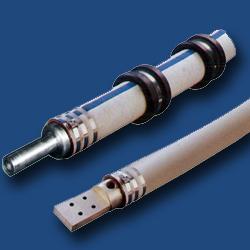
Cable water heater
Cable water heater The water heater cable is used to transfer electric power from the power source (frequency converter panel and capacitor bank) to the coil of the induction furnace. The constituent components of the water cooled cable Terminal: These terminal are generally designed in two forms: busbar or plate and threaded. The type of busbar that is more common in high power furnaces is made from a machined solid copper piece. These terminals have a number of holes on the flat side of the head, which are used to connect in the required place, and on the other end, they are mainly copper shafts with grooves and waterway.
بدون دیدگاه