What is an induction furnace?
An induction furnace is an electric furnace that uses the induction electrothermal effect of materials to heat or melt materials.The main components of an induction furnace are sensors, furnaces, power supplies, capacitors and control systems.
Under the action of the alternating electromagnetic field in the induction furnace, eddy currents are generated inside the material to achieve the effect of heating or melting. Under the stirring effect of this alternating magnetic field, the composition and temperature of the material in the furnace are relatively uniform, the forging heating temperature can reach 1250°C, and the melting temperature can reach 1650°C.
In addition to being heated or melted in the atmosphere, the induction furnace can be heated or melted in a vacuum and a protective atmosphere such as argon or helium to meet special quality requirements. Induction furnaces have outstanding advantages in diathermy or melting soft magnetic alloys,
high resistance alloys, platinum group alloys, heat resistant, corrosion-resistant, wear-resistant alloys, and pure metals. Induction furnaces are generally classified into induction heating furnaces and melting furnaces. Induction furnaces are generally classified into induction heating furnaces and melting furnaces.
An electric furnace that heats materials using an induction current produced by an induction coil. If the metal material is heated, it is placed in a crucible made of refractory material. If the non-metallic material is heated, the material is placed in a graphite crucible. When the AC frequency is increased, the induced current frequency is increased accordingly, and the amount of heat generated is increased. The induction furnace is heated quickly, the temperature is high, the operation and control are convenient, the material is less polluted during the heating process, and the product quality can be guaranteed. It is mainly used for melting special high-temperature materials, and also as a heating and control device for growing single crystals from the melt.The melting furnace is divided into two types: a core induction furnace and a coreless induction furnace.The core induction furnace has a core through the inductor and is powered by a commercial frequency power supply. It is mainly used for the melting and heat preservation of various cast iron, brass, bronze, zinc, and other metals.
The electrical efficiency is over 90%, and the waste furnace can be used. The smelting cost is low, and the maximum furnace capacity is 270 tons. The coreless induction furnace has no iron core passing through the inductor and is divided into a power frequency induction furnace, a triple frequency induction furnace, a generator set intermediate frequency induction furnace, a thyristor intermediate frequency induction furnace, and a high-frequency induction furnace.
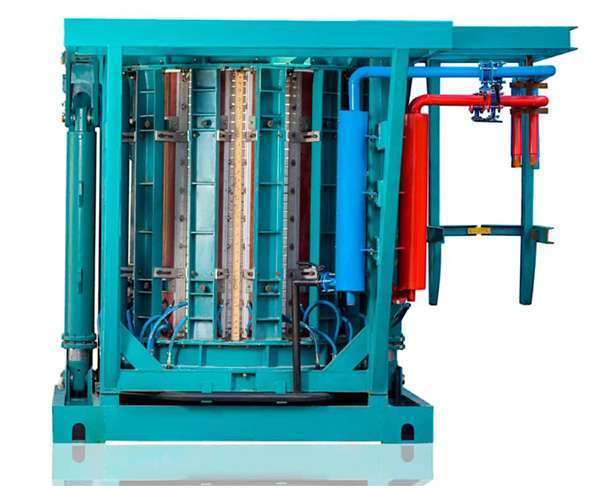
Types of induction furnaces
• Direct core
The direct core type induction furnace is shown ion fig. It consist of an iron core, crucible and primary winding connected to an power supply. The charge is kept in the cruicible, which forms a single turn short circuited
secondary circuit. The current in the charge is very high in the order of several thousand amperes. The charge is magnetically coupled to the primary coil. The change is melted because of high current induced in it. When there is no molten metal, no current will flow in the secondary. To start the furnace molten metal is poured in the oven from the previous charge.
This type of furnace has the following drawbacks:
The magnetic coupling between the primary and secondary is very weak, therefore the leakage reactance is very high. This causes low power factor. Low frequency supply is necessary because normal frequency causes turbulence of the charge.
If current density exceeds about 5 amps/mm2 the electromagnetic force produced by this current density causes interruption of secondary current. Hence the heating of the metal is interrupted. It is called pinch effect.
The crucible for the charge id of odd shape and inconvenient from the metallurgical point of view. The furnace cannot function if the secondary circuit is open. It must be closed. For starting the furnace either molten metal is poured into the crucible or sufficient molten metal is allowed to remain in the crucible from the previous operation. Such furnace is not suitable for intermittent services.
Indirect core type induction furnace:
In this type of furnace induction principle has been used for heating metals. In such furnace an inductively heated element is made to transfer its heat to the charge. When the primary winding is connected to the supply, current is induced in the secondary of the metal container. So heat is produced due to induced current. This heat is transmitted to the charge by radiation. The portion AB of the magnetic circuit is made up of a special alloy and is kept inside the chamber of the furnace.
The special alloy will loose its magnetic properties at a particular temperature and the magnetic properties are regained when the alloy will cooled. As soon as the furnace attains the critical temperature the reluctance of the magnetic circuit increases many times and the inductive effect correspondingly decreases thereby cutting off the heat supply. The bar AB is removable type and can be replaced by other, having different critical temperature. Thus the temperature of the furnace can be controlled very effectively.
Coreless induction furnace:
Coreless induction furnace also operates on the principle of transformer. In this furnace there is no core and thus the flux density will be low. Hence for compensating the low flux density, the current supplied to the primary should have sufficiently high frequency. The flux set up by the primary winding produces eddy currents in the charge. The heating effect of the eddy currents melts the charge. Stirring of the metals takes place by the action of the electromagnetic forces. Coreless furnace may be having conducting or non conducting containers. Fig shows a coreless induction furnace in which container is made up of conducting material. The container acts as secondary winding and the charge can have either conducting or non conducting properties. Thus the container forms a short circuited single turn secondary. Hence heavy current induced in it and produce heat. The flux produced by the primary winding produces eddy currents in the charge. The heating effects of the eddy currents melt the charge. Stirring action in the metals takes place by the action of the electromagnetic forces.
بدون دیدگاه